Truck Wheel Bearing Replacement: When to Service 18-Wheeler Hubs
Truck Wheel Bearing Replacement: When to Service 18-Wheeler Hubs
Blog Article
Keeping your trucks running smoothly isn't complicated. The key lies in regular maintenance checks, spotting concerns before they escalate, tracking fleet condition, and implementing proactive approaches. Regular inspections and repairs guarantee optimal uptime, improved performance, and protection. Direction from specialists from experienced technicians will guide you through fleet maintenance through the effective use of technology, detailed logging, and skilled personnel. Dive into this complete guide to fleet maintenance and discover cost-effective operations. There's plenty to learn and understand!
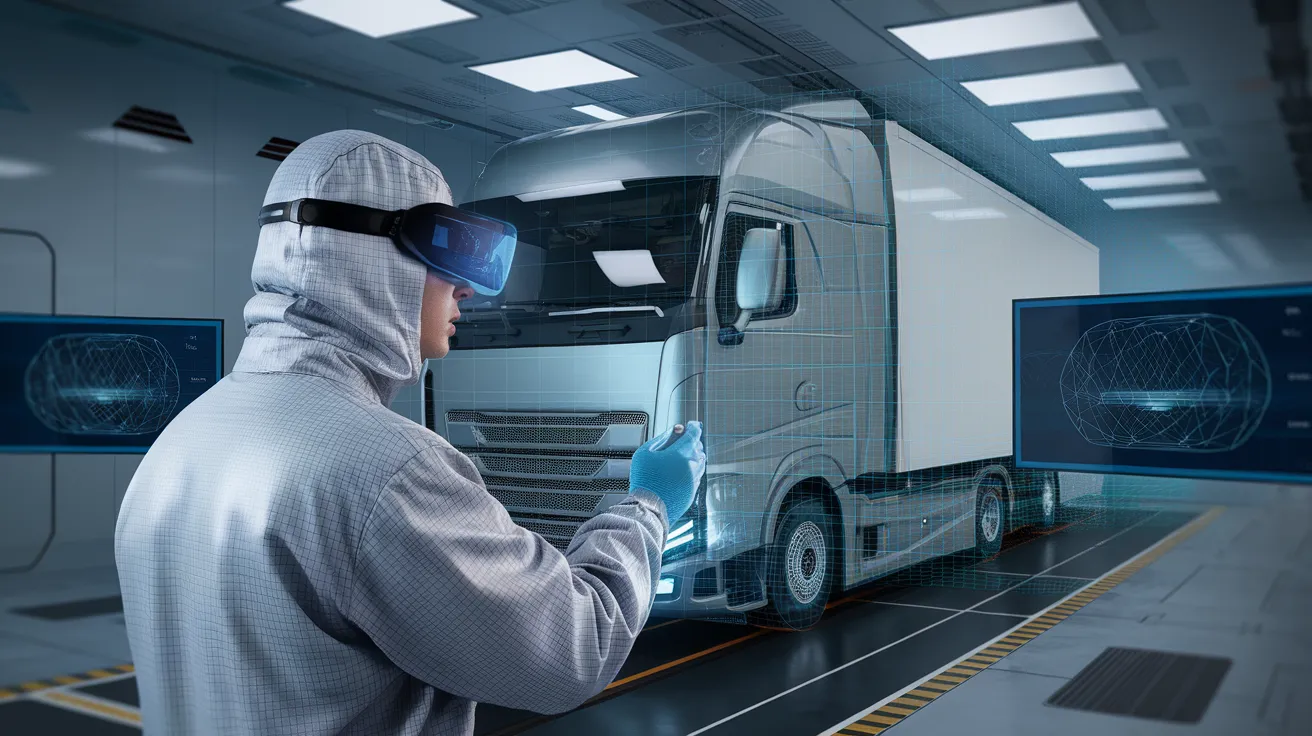
Main Insights
Understanding the Critical Role of Scheduled Fleet and Truck Maintenance
Though it could feel overwhelming, understanding proper fleet and truck maintenance is vital for any thriving operation. You'll discover the maintenance benefits far exceed the resources you put in. Consistent checks and upkeep can substantially prolong your vehicles' longevity, preventing expensive replacements. Furthermore, there's an obvious relationship between well-maintained trucks and better fuel economy. This results in reduced gas expenses, boosting your total operational efficiency. Moreover, frequent maintenance can detect small problems before they become serious problems, preventing costly repairs down the line. Therefore, don't underestimate the value of scheduled servicing; it can be a true difference-maker for your business's bottom line.
Understanding Fundamental Parts of a Effective Upkeep System
To ensure your fleet's performance and lifespan, it's essential to pinpoint the vital elements of a well-designed maintenance program. You'll have to grasp the core components of maintenance, assess the status of your fleet regularly, and establish preventive measures ahead of time. With these implemented, you're ready to minimizing downtime and enhancing productivity.
Essential Program Maintenance Aspects
If you're looking to improve your fleet's performance and durability, creating a solid maintenance program is vital. Critical elements of the program encompass regular inspections, regular servicing, and preventive repairs. Each aspect plays a crucial role in minimizing expensive failures and limiting downtime. While the rewards of a maintenance program are significant, it's important to address the implementation challenges. These often involve resource constraints and staff resistance. However, with strategic organization, effective messaging, and focus on skill development, these barriers can be addressed. Don't forget that an successful maintenance program isn't just about repairs; it stops them from occurring. It's an commitment in your fleet's future – and it's one that will yield significant returns.
Asset Performance Monitoring
When examining the key elements of a well-designed maintenance program, acknowledging the importance of fleet condition monitoring takes center stage. It's not just about maintaining operational vehicles, it's about enhancing fleet performance. Fleet monitoring systems provide a thorough view of your fleet's status, allowing you to spot potential issues before they escalate.
These monitoring systems track vital parameters like fuel performance, tire health, engine health, and more. By leveraging this data, you're not only ensuring the longevity of your fleet but also saving on avoidable maintenance expenses. Remember early detection is key in fleet management. Thus, adopt trustworthy monitoring technologies and keep ahead of the curve. Avoid simply responding to problems, predict them. Monitor your fleet's status regularly and your business will perform optimally.
Establishing Preventive Protocols
While keeping tabs on your fleet's condition is essential, establishing preventive protocols is equally critical to secure a effective maintenance program. It's important to detect potential concerns before they transform into costly repairs or downtime. So, let's talk preventive measures.
An important approach is establishing a detailed maintenance checklist. This document should detail all necessary examinations, tune-ups, and parts renewal. Regular engine inspections, tire servicing, and oil changes are fundamental. But don't overlook smaller components like wiper blades, illumination, and filter components.
Your maintenance plan needs to include a schedule for every maintenance item. Following this schedule ensures that your fleet remains in peak condition. Keep in mind, proactive maintenance reduces time, money, and headaches down the road.
Critical Regular Inspections for Truck and Fleet Maintenance
To guarantee your vehicles continue to be in top condition, you need to prioritize regular maintenance checks. These checks encompass regular service evaluations and critical component assessments. By following these essential procedures, you'll maximize your fleet's longevity, enhance operational efficiency, and consequently, save on major repair expenses.
Planned System Examinations
Routine maintenance inspections are your best protection from unplanned vehicle and fleet malfunctions. These inspections offer you a chance to identify and resolve problems before they develop into costly repairs or dangerous accidents. One of the primary scheduled maintenance benefits is the reduction of operational delays, which can substantially influence your operation's performance and revenue.
Essential Component Inspections
Expanding upon the significance of scheduled maintenance inspections, let's move towards the specific essential component checks that should be carried out regularly to ensure maximum truck and fleet performance. Start with the brake system – verify all components are working properly, from brake pads to fluid levels, as well as checking for leaks. Neglected, brakes may malfunction, leading to devastating incidents. Tire pressure checks are equally important. Underinflation elevates fuel consumption and tire wear, while excessive pressure may lead to a blowout. Invest in a reliable pressure gauge for exact readings. Keep in mind tires should be cold during checks for optimal results. Consistently conducting these important checks can save you from costly repairs and potential accidents. Maintain safety on the road.
Fleet Efficiency: Preventative Maintenance Best Practices
When managing a fleet, it's essential that you prioritize preventative maintenance to ensure peak efficiency. Establishing a systematic preventative scheduling system is essential. This prevents unnecessary wear and tear, and reduces the chances of unscheduled downtime. You should schedule regular maintenance and inspections based on engine hours, mileage, time, or fuel usage. Keep in mind each vehicle is unique and might need a tailored approach.
Maintenance education serves as an essential method to secure peak efficiency. Give your personnel the essential skills to spot potential issues before they escalate. This reduces downtime but also minimizes expenses. The fusion of scheduled prevention and maintenance education will lead to a highly effective and trustworthy fleet. Proactive maintenance always trumps reactive repairs.
Crucial Pointers for Fleet and Truck Restoration and Repair
While vehicle fleet repair and restoration can seem overwhelming, understanding the process can make it much simpler. Your initial step needs to be to understand multiple restoration approaches. This expertise will help you identify issues effectively and promptly. Then, prioritize restoration projects depending on the extent of repairs needed and the unit's importance in your vehicle lineup. Frequently check every truck for developing concerns website and tackle them quickly to stop issues from worsening. Don't forget, restoration isn't just about fixing issues, it's focused on enhancing the truck's performance and lifespan. Finally, make sure to select top-grade materials for restoration; they'll last longer and perform better. Keep these tips in mind, and you'll navigate truck and fleet repair and restoration effectively.
Harnessing Technological Advances for Advanced Fleet Management
To remain competitive in the trucking industry, it's essential to harness industry innovations for enhanced fleet maintenance. Technological advancements are revolutionizing the maintenance landscape. Make use of data analytics to track your fleet's operations and anticipate maintenance needs in advance.
Advanced real-time tracking systems keep track of engine performance and health, fuel efficiency, and driving habits. Make use of these insights to schedule preventive maintenance, minimizing expensive downtime.
Don't overlook software updates. They usually include critical updates and fixes that optimize your vehicles' safety and performance. Note that fleet management goes beyond mechanical care. You're working in a modern period, and adapting to technological advances will promote your fleet's sustainability and profitability. By utilizing effective procedures, you can minimize time and money, and safeguard human life.
Frequently Asked Questions
What Skills Should a Skilled Vehicle Fleet Mechanic?
You will require a proper certification, meeting the standards of an established mechanic institution. Furthermore, you require a comprehensive skill assessment, showing your knowledge in multiple facets of fleet maintenance and repair. Prior experience is essential!
When Should I Change the Tires on My Fleet Vehicles?
Similar to clockwork with the changing seasons, you should regularly check your fleet's tread depth on a consistent basis. Yet, it's generally recommended to install new tires every three to 6 years, according to driving conditions and frequency of use.
What Are the Common Signs of Engine Trouble in Trucks?
You'll spot truck engine problems through indicators including strange engine sounds or reduced fuel economy. Additional indicators are heavy smoke emissions, engine oil drips, or a continuously lit check engine warning.
Does Technology Play a Role in Improving Truck and Fleet Maintenance?
Technology is crucial in improving truck maintenance. Telemetry systems deliver real-time data, while smart systems anticipate issues before they happen. You'll notice reduced downtime, enhanced security and in the end, financial benefits. It's transformative.
How Do Maintenance Needs Vary Across Fleet Vehicle Types?
Different vehicle types certainly require unique maintenance schedules. You need to consider the intended use, carrying capacity, and terrain type, as these factors significantly affect required servicing. Always adjust maintenance based on the type of vehicle.
Closing Remarks
When it comes down to it, the focus is on ensuring your fleet operates efficiently, right? Regular maintenance isn't just a suggestion, it's absolutely necessary. By pinpointing crucial elements, carrying out systematic evaluations, using preventative strategies, and leveraging technological advances, you're doing more than basic maintenance, you're developing a high-performance fleet. And don't forget, truck and fleet repair isn't a failure, it's a pathway to enhancement. Stay committed, and you'll experience your fleet's efficiency, reliability, and longevity achieve new levels.
Report this page